Jak powstaje smartfon? Wydaje się proste, prawda? Jest sobie taśma produkcyjna, na której dodawane są kolejne elementy. Tu bateria, tam wyświetlacz, a na koniec obudowa i voila. Widziałem cały proces na własne oczy i jest kilka smaczków, którymi chciałbym się z Wami podzielić.
Jak powstaje smartfon? Byłem w jednej z najnowocześniejszych fabryk na świecie
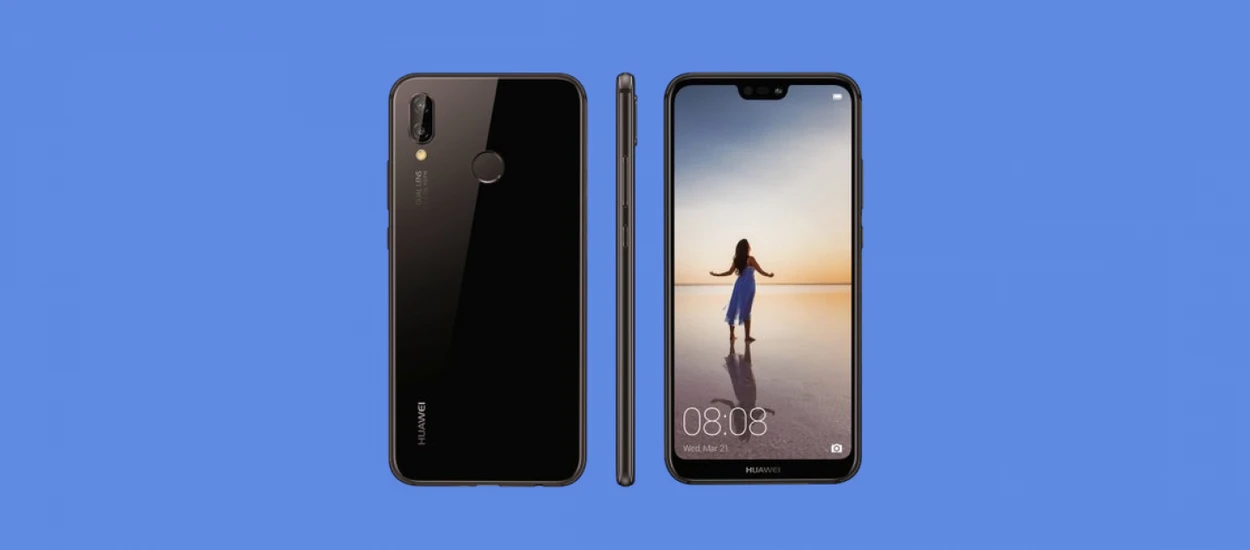
Położona nieopodal Shenzhen, w chińskiej prowincji Dongguan siedziba firmy to kompleks składający się z wielu hal produkcyjnych. Miałem przyjemność zajrzeć do jednej z nich i zobaczyć na własne oczy, jak powstają smartfony Huawei - konkretnie modele P20.
Niestety, musicie mi wierzyć na słowo, bo robienie zdjęć wewnątrz jest zabronione. Przed wejściem otrzymuje się specjalny strój składający się z białego kitla, żółtej czapeczki z daszkiem i obuwia ochronnego (sandałów - w moim przypadku o jakieś dwa rozmiary za małych). Wszystkie metalowe przedmioty należy zostawić w depozycie. Na halę wchodzimy bowiem przez bramki z bardzo wrażliwymi czujnikami - ich działanie można śmiało porównać do tych, które spotyka się na lotniskach.
Na hali znajduje się kilka taśm produkcyjnych - każda o długości ok. 150 metrów. Każda posiada też duży ekran informujący o normach, jakie powinna wyrobić dana taśma, ilości błędów i liczbie produkowanych smartfonów.
Zaczynamy od podstaw, a więc płyty głównej. Jej konstrukcja odbywa się w sposób całkowicie zautomatyzowany. Płyty są tworzone w parach. Na początkowych etapach umieszcza się na nich poszczególne moduły, których jest łącznie kilkadziesiąt. Mowa tutaj m.in. o procesorze, pamięci, modemie LTE, antenie WiFi itd. Co ciekawe, moduły te mają formę wielkich szpul przypominających trochę klisze fotograficzne. Z daleka wygląda to tak, jakby na każdej szpuli znajdowała się taśma. Podchodząc bliżej, łatwo zauważyć, że to tak naprawdę np. procesory Kirin 970. Maszyna "pożera" taśmę, a z wewnątrz wydobywają się głuche odgłosy - poszczególne moduły są wlutowywane w płyty główne.
Konstrukcja idzie dalej. Mechaniczne ramiona instalują metalowe pokrywy, które mają nie tylko chronić podzespoły, ale też odprowadzać ciepło. W międzyczasie płyty są rozcinane na dwa odrębne elementy. Każdy trafia do osobnego smartfona.
W końcu pojawiają się ludzie - na całej linii produkcyjnej jest ich zaledwie 20. Wcześniej liczba pracowników sięgała 150. Huawei jednak sam skonstruował maszyny, które ich zastąpiły. Efekty robią duże wrażenie. Tu mechaniczne ramię podłącza baterię, tam instaluje obudowę. Poszczególne etapy wymagają niezwykłej precyzji, a maszyny nie tylko ją gwarantują, ale też ograniczają do niemal zera ryzyko popełnienia błędów.
2-3 godziny później smartfon jest gotowy. W większości to zasługa maszyn. Choć ciągle jest kilka czynności, jak np. instalacja wyświetlacza, gdzie sprawy w swoje ręce musi wziąć człowiek.
Wydawać by się mogło, że na tym koniec. A tymczasem to zaledwie jedna dziesiąta czasu potrzebnego na wyprodukowanie jednego urządzenia. Urządzenie spędza bowiem aż 30 godzin na taśmie, gdzie jest testowane. Poddaje się je na działanie niskich i wysokich temperatur. Badana jest też odporność uszkodzenia. Mechaniczne ramiona wciskają przyciski power i sprawdzają responsywność wyświetlacza. Na innym stanowisku wywoływana jest paleta kolorów, a kamery w maszynach sprawdzają, czy jest ona wystarczająco dobra. Maszyny testują nawet aparat - kontrolując występowanie dystorsji czy artefaktów.
I tutaj jednak są scenariusze, w których nie udało się całkowicie wyeliminować człowieka. Na jednym stanowisku pracownik przykleja folie ochronne na wyświetlacz. Na innym, zamknięty w szklanym, wygłuszającym boksie człowiek sprawdza działanie głośnika. Jest też ktoś odpowiedzialny za kontrolowanie działania mikrofonu - mówi coś do niego, a następnie odsłuchuje nagranie. Brzmi strasznie archaicznie, prawda? Najwyraźniej to ciągle najskuteczniejszy sposób testowania.
Taką procedurę testową przechodzi każdy model. Zatem, kiedy wyjmujemy go z pudełka, ma on już za sobą 30 godzin naprawdę intensywnego działania. Tylko w taki sposób producent może się upewnić, że nie wprowadzi na rynek wadliwego produktu. 30 godzin to naprawdę dużo.
Końcowe etapy, a więc pakowanie do pudełka, również maksymalnie zautomatyzowano. Choć do naklejania folii wykorzystywany jest pracownik, maszyna odpowiada za jej wyrównanie i brak bąbelków powietrza pod spodem. Maszyna też przygotowuje pudełko, zawija je w folię i dostarcza do kolejnego pracownika, który przykleja na pudło naklejki z numerem seryjnym oraz numerami IMEI. Finalnie całość pakuje się w kartony liczące po 10 smartfonów. Z końca taśmy odbiera je... robot - sam je sobie ładuje, a następnie przygrywając wesołą melodią (ach ci Chińczycy...) odjeżdża do magazynu.
Mimo tak wymagających procedur każdego dnia z taśmy produkcyjnej zjeżdża 2800 smartfonów. Pracownicy pracują na kilka zmian, a więc tak naprawdę taśma działa bez przerwy. Całość jest na tyle klarowna, że w przypadku błędu, możliwe jest łatwe zidentyfikowanie, w którym miejscu i przez kogo został on popełniony. Jak jednak zapewniano - od pół roku żadnego błędu nie było.
Praca przy produkcji smartfonów Huawei zapewne nie należy do najprostszych, ale dla Chińczyków jest pewnym prestiżem. Oczywiście są to deklaracje trudne do zweryfikowania, ale po warunkach panujących wewnątrz można łatwo wywnioskować, że tak właśnie jest.
Dla mnie zobaczenie procesu powstawania smartfona na własne oczy było niewątpliwie ważnym doświadczeniem i ciekawym przeżyciem. Okazuje się, że tworzenie nowych technologii ciągle nie może odbywać się w sposób w pełni zautomatyzowany, ale jesteśmy zaledwie o krok od wejścia na ten poziom. Imponujący jest natomiast stopień precyzji, jaki towarzyszy całości, a także kładzenie tak dużego nacisku na testy i kontrolę jakości. Najwyraźniej Huawei nie zamierza nigdy dopuścić do sytuacji, w której, z bliżej nieokreślonych powodów, znaleźli się konkurenci.
Hej, jesteśmy na Google News - Obserwuj to, co ważne w techu